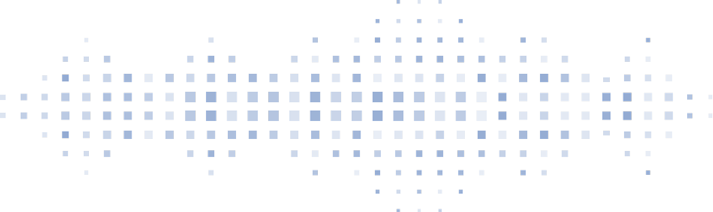
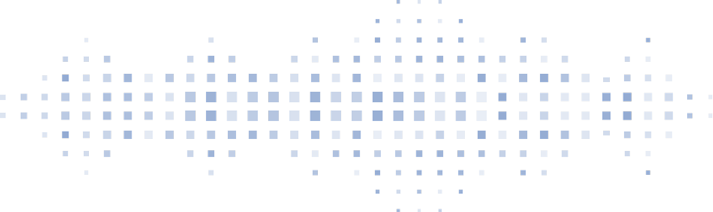
News5 Key Features Every Drilling Machine Should Have for Maximum Efficiency
5 Key Features Every Drilling Machine Should Have for Maximum Efficiency
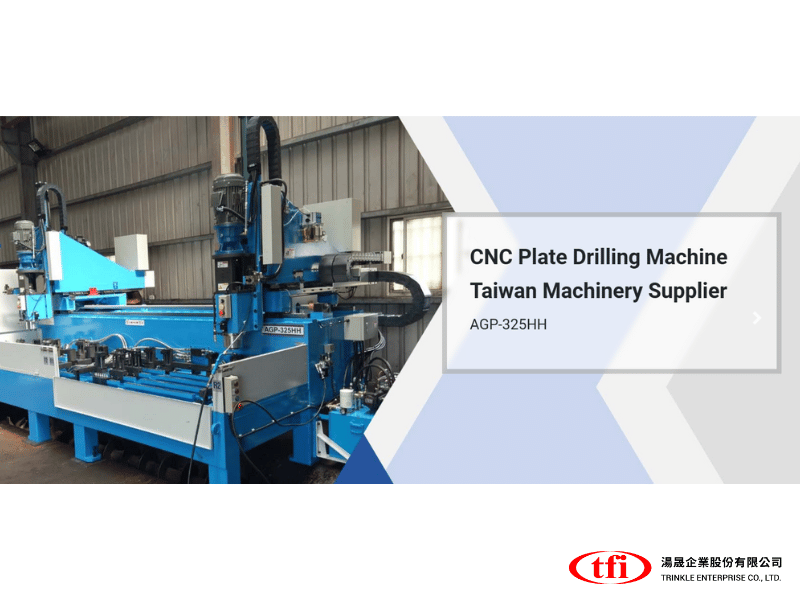
Introduction
In the world of industrial manufacturing, drilling machines are indispensable tools, essential for creating precise holes in materials ranging from metals to composites. However, not all drilling machines are created equal. To ensure maximum efficiency and productivity, a drilling machine must possess specific features that enhance precision, reduce downtime, and optimize operations. This article explores five key features every modern drilling machine should have to meet the demands of today’s industries.
1. Advanced CNC Control System
Why It Matters:
An advanced CNC (Computer Numerical Control) system is the backbone of any modern drilling machine. It provides precise control over the drilling process, allowing operators to automate complex tasks with ease. With CNC, manufacturers can program exact hole dimensions, depths, and patterns, ensuring consistency and reducing errors.
Benefits:
- Enhanced precision for high-quality results.
- Ability to handle complex drilling patterns.
- Increased productivity with automation capabilities.
Example:
CNC-controlled machines, like those offered by Trinkle Enterprise Co., Ltd., ensure precise and repeatable operations, making them ideal for industries such as aerospace and automotive manufacturing.
2. Hydraulic or Servo-Driven Spindle System
Why It Matters:
The spindle system is crucial for delivering consistent power and precision during drilling. Hydraulic or servo-driven spindles provide better control over speed and force, ensuring optimal performance for different materials and thicknesses.
Benefits:
- Smooth and controlled feeding for consistent drilling.
- Reduced wear and tear on tools, increasing their lifespan.
- Improved adaptability to various materials, from steel to lightweight alloys.
Example:
The hydraulic feeding system in Trinkle's DNC series machines mimics servo control, offering near-servo precision at a lower cost while maintaining excellent performance.
3. Quick-Change Tool System
Why It Matters:
Tool changing can be a significant source of downtime in manufacturing operations. A quick-change tool system minimizes this by allowing operators to switch drill bits in seconds, improving overall productivity.
Benefits:
- Faster tool changes reduce machine downtime.
- Easier tool management for operators.
- Enhanced compatibility with various tool types.
Example:
The BT-40 Quick-Change Shank, featured in Trinkle’s drilling machines, allows operators to load and remove drill bits in just one second, dramatically improving efficiency while reducing tool costs.
4. Integrated Measuring Systems
Why It Matters:
Integrated measuring systems ensure accurate drilling by automatically adjusting for tool length, material thickness, and cutting depth. These systems eliminate the need for manual calibration, saving time and reducing the likelihood of human error.
Benefits:
- Precise control over drilling depth and position.
- Automatic adjustments for consistent results.
- Reduced setup time for faster operations.
Example:
Trinkle’s patented thickness-measuring encoder adjusts cutting modes (heavy-cutting, light-cutting, or blank-cutting) in real-time, ensuring the best cutting efficiency for each job.
5. Durable and User-Friendly Design
Why It Matters:
A drilling machine must be built to last while being easy to operate and maintain. High-quality materials, ergonomic controls, and modular designs all contribute to a machine’s longevity and ease of use.
Benefits:
- Increased machine lifespan reduces overall costs.
- Simplified maintenance minimizes downtime.
- User-friendly controls improve operator productivity and safety.
Example:
Trinkle’s drilling machines feature an independent hydraulic cylinder design, simplifying maintenance and reducing service time, ensuring the machine stays operational longer.
Conclusion
Investing in a drilling machine with these five key features—an advanced CNC control system, a hydraulic or servo-driven spindle system, a quick-change tool system, integrated measuring systems, and a durable, user-friendly design—ensures maximum efficiency, precision, and reliability. These features not only optimize production but also reduce operational costs, making them essential for any modern manufacturing operation.
Trinkle Enterprise Co., Ltd. is proud to offer cutting-edge drilling machines equipped with all these features, designed to meet the diverse needs of industries worldwide. Whether you’re in construction, aerospace, or automotive manufacturing, Trinkle’s innovative solutions ensure your operations run at peak efficiency.
For more information about our products, visit Trinkle Enterprise Co., Ltd..